Vladislav Medvedovskyi, Softarex Technologies, Inc.
Alexander Lipanov, Ph.D. in Computer science, Softarex Technologies, Inc.
What is Industry 4.0?
Industry 4.0 stems from the realization that a 4th industrial revolution is upon us. Industry 4.0 is like a fancy trend that everyone discusses but can’t give a precise definition. Besides, hardly anyone distinguishes the difference between Industry 4.0 and the Internet of Things. All we can say for sure is that Industry 4.0 stands on the intelligent connectivity of smart devices by which objects can sense one another and communicate. Industrial production machinery no longer just “processes” the product. The product itself communicates with the machinery, using smart sensor devices, to give precise instructions.
Manufacturing companies are currently implementing this “intelligent connectivity of smart devices” in their factories and on the shop floor.
Our Equipment Maintenance Software brings this concept to life by using IoT sensors, computer vision and neural networks to enable real-time monitoring and predictive maintenance in complex manufacturing environments.
Why is it happening?
Competition is a King. Today being successful means being highly competitive. That’s why variety and prompt innovation are in great need. The growth of production and range of its constant modification is an indispensable condition for the development of the industrial business. Everything that is manufactured needs to be demanded, otherwise, it’s too risky. Therefore it is highly important to offer the market a variety while producing only what is requested. Sales growth leads to the growth of assortment and it generates a huge amount of information that needs to be kept up-to-date for reuse again in sales. All that leads us to the potential benefits and competitive advantage for multinational industrialists who will be the first to implement Industry 4.0.
Is it really happening?
Industry 4.0 seems so promising and no one doubts about its prospects. But implementing it into practice usually is a matter of the future — maybe not too distant, but still the future. Today business people care about other more urgent issues.
But the report The Internet of Things business index: A quiet revolution gathers pace sponsored by ARM and edited by the Economist Intelligence Unit has shown that three-quarters of companies leading in the planetary economy already somehow use “Internet of things”. Future is Now!
Implementation of Industry 4.0 involves the computerization of the entire production environment. It means the integration of cyber-physical systems (or CPS) with production processes and logistics, as well as the active use of the Internet in manufacturing processes.
Advantages that Industry 4.0 brings
The great advantage of Industry 4.0 is that it can be implemented step by step. Using cyber-physical systems companies can transform manufacturing without stopping the process. This involves the necessary sensors equipment, the installation of the system components with miniature servers, and the replacement of the bus system. That is, you can start with a single machine, and then convert the entire plant. What is said about the “fourth industrial revolution” is actually an evolution of machines. Hough Industry 4.0 isn’t still implemented on an industrial scale, the partners from research organizations and industrial sectors are working hard to make it a reality.
Moreover, remote device management and monitoring create a plethora of efficiency-improving opportunities for businesses, such as:
- Reduction of operating costs related to hardware status monitoring and 24/7 monitoring of any devices and components.
- Dynamic, intellectual manufacturing planning and load balancing systems help to reduce operating expenses.
- Possibility to aggregate data from several companies/factories in a single Data Center.
- Selling devices as a service — you can sell a device including monitoring and maintenance services by subscription.
Industry 4.0: how it works
No better way to understand Industry 4.0 than create it. We at Softarex Technologies, Inc. prepared a small prototype of the indoor air quality control system as an example of Industry 4.0 capabilities. Let’s call it simply “The system”. The most interesting thing, in this case, is that system can be created and scaled easily. For prototyping, an ordinary Lego kit was used. The system itself is a set of devices communicating via a central server. The server is the “command center” for the entire system and is responsible for its correct operation. To make it more convenient the system also has a portal for users who want to monitor the system status online.
The system demonstrates an approach where a network unites both devices developed from scratch and existing devices retrofitted to support communications with the server. It helps to demonstrate the viability of the Industry 4.0 approach, which states that it is unnecessary to renew the entire hardware base — instead, existing hardware can be upgraded to support network connectivity and remote management functionality. Apart from this usage of relatively cheap, compact, and autonomous components makes the transition to the Industry 4.0 paradigm affordable and efficient.
The system includes the following components:
- Central server
- Gas and dust sensor
- Cooling device
- Image printer
- Mobile phone with a camera for taking pictures and sending them to the printer
- Operator’s portal

Main principles of system operation
The core of the system is a server that is used for manufacturing process control. The server receives print requests from the operator. A person takes photos by mobile phone and then sends them to the printer. In case there are no available printers, photos are added to the queue till one becomes available. The status of each request and the current queue can be viewed on the operator’s portal.
We’ve created a special application for printer interaction. It communicates with the server via the Web Sockets protocol. The app exchanges data with the printer via Bluetooth, it receives commands from the server and converts them into Bluetooth commands for the printer. The printer, in turn, prints images upon receiving commands from the app.
In the same room where the printer is located, there is also a gas and dust sensor. For example, usually, the following gases are detected: H2, C2H5OH, and CO. Once a minute, the sensor submits information about the composition of the atmosphere to the server and also publishes it to the operator’s portal. In case one of the 4 measured values exceeds a set threshold, the corresponding sensor sends an alarm signal and triggers the alarm mode. In this mode, the sensor sends data to the server every second. When the server receives an alarm signal, it shuts down the printer and activates the cooling device.
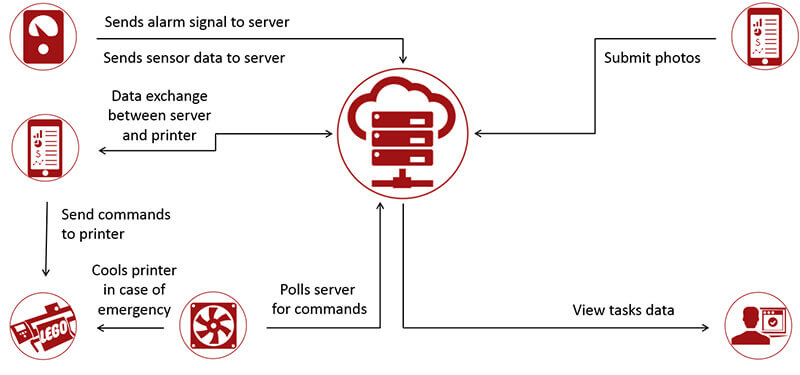
Details about used hardware and software
1. Server
We used Server REST API based on Play Framework 2.4.x. Redis was used as data storage. The Jesque library is used for persistent task queues and commands.
The server includes three task queues: for the printer, cooling device, and alarm signals which have the highest priority among other queues.
The Publisher/Subscriber mechanism integrated into Redis was used for notifications generation about the completion of printing. The server subscribes to a completion event and the app controlling the printer generates it when the printer stops printing the current image (i.e. the printer queue is empty).
2. Gas/dust sensor
The gas and dust sensor is a device that consists of the following components:
- Arduino NANO controller
- ESP 8266-07 Wi-Fi module
- MQ-3 (C2H5OH) sensor
- MQ-7 (CO) sensor
- MQ-8 (H2) sensor
- Sharp GP2Y10 (dust) sensor
The sensors are connected to digital I/O pins on Arduino. The microcontroller collects data from sensors and sends it to the server. The Wi-Fi module provides wireless connectivity with the server. It is controlled with AT commands sent by the microcontroller via two digital I/O outputs using a software UART interface based on the SoftwareSerial library. This library is part of the microcontroller.
Sensor readings are sent to the server every minute. If any of them exceeds a threshold defined in the microcontroller’s firmware, the sensor generates an alarm signal and sends a corresponding message to the server.
3. Cooling device
The cooling device is based on ESP8266 — 07. The devices query the central server every second via the HTTP protocol. If the response is different from 200 OK, it applies voltage to GPIO outputs, thus enabling or disabling the fan.
4. Image printer
The image printer is based on Lego Mindstorms NXT 2.0 set. It is controlled via a Bluetooth adapter connected to a PC/laptop next to the printer. Printing is carried out with the help of a marker that is moved by the printer’s servos. The server generates commands for the device using a special protocol. The printer uses A4 paper sheets.
Please, note that the device was assembled for demo purposes.
In other conditions, the printer can be replaced with any other network-enabled device (for direct communication with the server) or a Bluetooth-enabled device (in this case, communications with the server are performed using a device that is an intermediary between Bluetooth and a LAN/WAN network).
5. Mobile phone with a camera for sending images to the printer
An Android-based phone was selected as the source of images for the system. Thanks to simple Android app photos were taken via a built-in camera. Afterward, they were sent to the server using HTTP POST requests. Due to task queues support, there is no possibility to send several photos at a time. All sent photos will be printed according to the general print queue. The server supports a random number of devices serving as image sources.
6. Operator’s portal
The operator’s portal is a website based on the JSF technology. It consists of two pages:
- Sign-in page
- Task listing page with task statuses
Before the work starts user had to log in. After it’s done successfully user will be redirected to the page with the tasks list and their current statuses. Task status can assume one of the following values: In progress, Queued, Completed successfully, Completed with an error.
The queue is updated in real time by connecting to the server through WebSockets, so there is no need to refresh the page each time you need actual information.
Instead of conclusion
What is the conclusion of this case? First of all, it shows that Industry 4.0 isn’t something incredibly futuristic. It can be implemented and what is more important it is scalable. The reason why Industry 4.0 isn’t still implemented ubiquitously is the lack of specific knowledge and skills in this area. Besides, a deficit of specialists and managers. Industry 4.0 is too young!
To succeed and gain a competitive advantage each company involved in manufacturing needs to focus on experts’ acquisition. Without such knowledge and experience, accelerated investment does not make sense. In case it can’t be done in-house then outsource, but not standing still. Make a move before it’s not too late.